Exploring Refractory Metals: The Essential Role of Tungsten and Molybdenum in Sustainable Industries
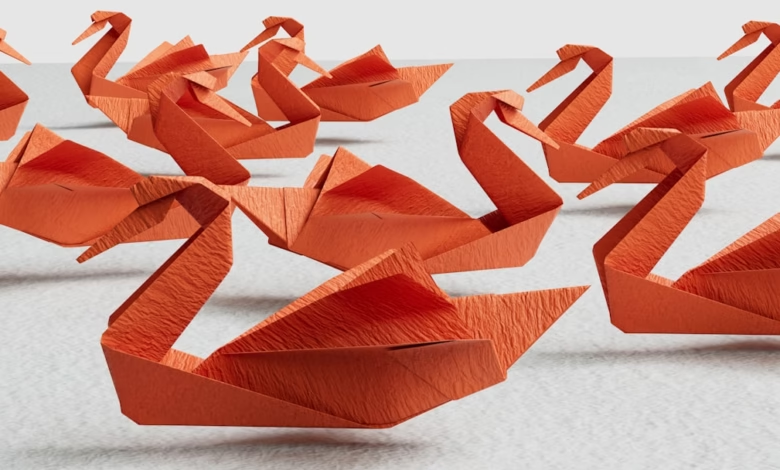
In the ever-evolving landscape of materials science, refractory metals have emerged as critical components in various high-performance applications. These unique metals, including tungsten and molybdenum, exhibit remarkable heat resistance, making them indispensable in industries where durability and reliability are paramount. As modern industries, such as aerospace and energy, continue to push the boundaries of technology, understanding the properties and applications of refractory metals becomes essential. This article delves into the fascinating world of refractory metals, exploring their significance in contemporary metallurgy and industrial practices, while also addressing the sustainable production and recycling challenges that accompany them. By examining the roles of tungsten and molybdenum, we highlight their contributions to sectors reliant on aerospace metals and energy metals, and consider the innovations shaping the future of metal recycling and sustainability in metal production. Join us as we uncover the vital role that these high-heat-resistant metals play in the broader context of metal commodities, from precious metals to base metals, and discover how they are paving the way for advancements in metal fabrication and 3D printing technologies.
- 1. Understanding Refractory Metals: Properties and Applications in Modern Industries
- 2. The Role of Tungsten and Molybdenum in Aerospace and Energy Sectors
- 3. Sustainable Production and Recycling of Refractory Metals: Challenges and Innovations
1. Understanding Refractory Metals: Properties and Applications in Modern Industries
Refractory metals, primarily consisting of tungsten, molybdenum, tantalum, and niobium, exhibit exceptional resistance to heat and wear, making them indispensable in various modern industries. These high-heat-resistant metals are characterized by their high melting points, typically exceeding 3000°C, which allows them to maintain structural integrity under extreme conditions. Unlike precious metals such as gold and platinum, refractory metals are classified as non-ferrous metals and are often utilized in applications where other industrial metals, like steel and aluminum, would fail.
In metallurgy, refractory metals are crucial for producing metal alloys that require enhanced durability and thermal stability. They play a significant role in sectors such as aerospace, where they are used in turbine engines and exhaust systems due to their ability to withstand high temperatures without degrading. Additionally, their resistance to metal corrosion makes them ideal for chemical processing applications, where harsh environments can lead to rapid material degradation.
The applications of refractory metals extend to the energy sector, particularly in the manufacture of components for nuclear reactors and in the development of battery metals for energy storage systems. With the increasing focus on sustainable metal production, these metals are also gaining traction in metal recycling initiatives, where their valuable properties can be recovered and reused, contributing to a circular economy.
As industries continue to evolve, the demand for refractory metals is expected to rise, aligning with current metal trends that emphasize efficiency and sustainability. Innovations such as 3D printing metals are enhancing the fabrication processes for refractory metals, allowing for more complex and efficient designs in automotive and aerospace applications. Moreover, the growing interest in rare earth metals, alongside base metals like copper and zinc, highlights the interconnected nature of these resources in modern metal mining.
In summary, the unique properties of refractory metals make them vital to various industrial applications, reinforcing their importance within the broader context of metal commodities and sustainable practices in the modern economy. Understanding their characteristics and potential uses is crucial for industries aiming to leverage the benefits of these remarkable materials.
2. The Role of Tungsten and Molybdenum in Aerospace and Energy Sectors
Tungsten and molybdenum are critical components in the aerospace and energy sectors due to their exceptional heat resistance and mechanical properties. As refractory metals, they are capable of withstanding extreme temperatures without losing their structural integrity, making them ideal for high-performance applications.
In aerospace, tungsten is often used in the manufacturing of aerospace metals, such as turbine blades and rocket nozzles. Its high melting point and density contribute to the durability and efficiency of components that operate under intense heat and pressure. Molybdenum, on the other hand, is utilized in various aerospace applications, including aircraft engines and missile components, due to its strength and resistance to metal corrosion, ensuring reliability in challenging environments.
In the energy sector, both tungsten and molybdenum play essential roles in the production of metal alloys used in nuclear reactors and fossil fuel power plants. Tungsten is often found in components that require excellent thermal conductivity and resistance to thermal expansion, while molybdenum is used to enhance the strength and toughness of steel and other base metals that are critical in energy infrastructure.
Furthermore, as industries increasingly focus on sustainable metal production and metal recycling, the demand for these refractory metals continues to grow. The mining of tungsten and molybdenum, often classified as industrial metals, is vital for ensuring a steady supply of these materials for future applications. With the rise of new metal trends, including metal fabrication technologies such as 3D printing, the versatility of tungsten and molybdenum is becoming more apparent. Their unique properties make them an attractive choice for innovative designs and efficient manufacturing processes in both aerospace and energy sectors.
In conclusion, the importance of tungsten and molybdenum cannot be overstated, as they are essential to the advancement of aerospace and energy technologies. As a result, ongoing research and development in metallurgy and metal commodities will likely further enhance their applications, paving the way for improved efficiency and performance in these critical industries.
3. Sustainable Production and Recycling of Refractory Metals: Challenges and Innovations
The production and recycling of refractory metals, such as tungsten and molybdenum, present unique challenges and opportunities in the realm of sustainable metal production. As industries increasingly seek to minimize their environmental impact, the focus on sustainable practices in metallurgy is paramount. Refractory metals are essential in high-temperature applications across various sectors, including aerospace, automotive, and energy, which makes their sustainable sourcing and recycling vital.
One of the primary challenges in the sustainable production of refractory metals lies in the metal mining process. Extracting these industrial metals often requires significant energy and generates considerable waste, impacting the surrounding environment. Furthermore, the mining of rare earth metals, which are often found alongside refractory metals, can exacerbate these environmental concerns. Innovations in extraction technologies, such as bioleaching and sustainable mining practices, are emerging to mitigate these impacts, ensuring that the demand for metals like tungsten and molybdenum can be met with reduced ecological footprints.
Metal recycling plays a crucial role in addressing these challenges. Although refractory metals are not as widely recycled as base metals like aluminum and copper, advancements in metal fabrication techniques are paving the way for more efficient recycling methods. The development of specialized processes to recover and refine these high-heat-resistant metals can significantly reduce the need for new metal mining, conserving resources and energy. Additionally, the integration of 3D printing metals technology allows for the creation of complex components from recycled refractory metals, promoting a circular economy.
In the context of metal trends, the push for sustainability has led to increased investment in research and development. Industries are exploring new alloy compositions that enhance the recyclability and performance of refractory metals, while also reducing reliance on precious metals like platinum and palladium. Furthermore, the growth of battery metals and their applications in energy storage systems has created a demand for innovative recycling solutions that can reclaim valuable materials without contributing to metal corrosion or degradation.
In conclusion, the sustainable production and recycling of refractory metals present both challenges and innovations. As industries continue to evolve, the integration of sustainable practices in the supply chain, coupled with advancements in metallurgy and metal recycling technologies, will be critical in ensuring that these essential materials can meet future demands while minimizing environmental impacts.
In conclusion, refractory metals like tungsten and molybdenum play a crucial role in various high-demand industries, particularly aerospace and energy sectors. Their unique properties make them indispensable in applications where heat resistance and durability are paramount. As industries continue to evolve, understanding the metallurgy of these industrial metals is essential for innovation and performance.
Moreover, the sustainable production and recycling of refractory metals present both challenges and opportunities for the future. As we move towards a more sustainable approach in metal mining and metal fabrication, finding ways to incorporate metal recycling and reduce the environmental impact of extraction processes will be key. This aligns with broader trends in the metal commodities market, where there is increasing interest in sustainable metal production and the responsible sourcing of precious and rare earth metals.
As we explore advancements in 3D printing metals and the integration of battery metals for energy solutions, the significance of refractory metals in shaping the future of construction metals and automotive metals cannot be overstated. For investors and industries alike, staying informed about the dynamics of metal trends and the potential of these high-heat-resistant metals will be essential for strategic decision-making in a rapidly changing market. Ultimately, the ongoing development and application of refractory metals will not only enhance industrial capabilities but also contribute to a more sustainable future in metallurgy.