Mastering Your Finances: Essential Strategies for Budgeting, Saving, and Investing in Your Future
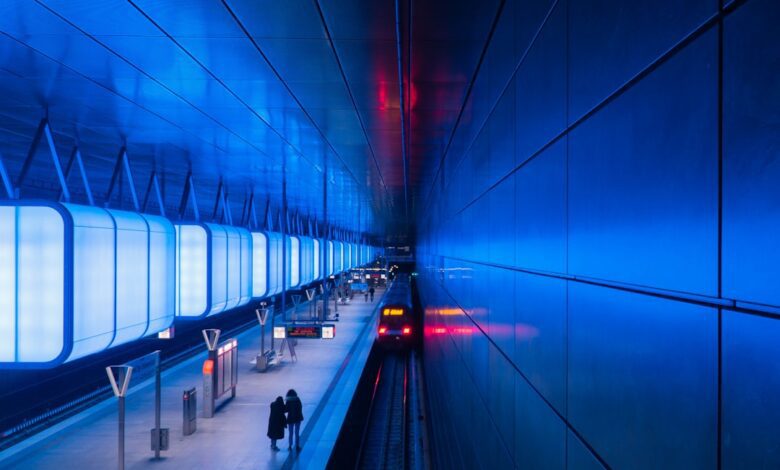
In today's fast-paced financial landscape, mastering the art of budgeting is more crucial than ever. Whether you're a recent graduate stepping into the workforce or a seasoned professional looking to enhance your financial literacy, effective personal finance management can lead to greater security and peace of mind. This article offers essential budgeting tips that can help you navigate the complexities of personal finances with confidence.
We'll explore how to build a robust emergency fund to safeguard against unexpected expenses, develop strategies for paying off debt and improving your credit score, and emphasize the importance of retirement planning as a cornerstone of long-term financial health. Additionally, we'll discuss the value of investing in yourself through education and skill-building, uncover savvy tax-saving strategies, and highlight the role of insurance in protecting your financial future. Finally, we’ll provide guidance on setting and achieving long-term financial goals that align with your aspirations. Join us on this journey to financial empowerment, where each step taken today paves the way for a more secure tomorrow.
- Here are three possible section headlines for your article on budgeting tips for managing personal finances effectively:
- 1. **Building a Strong Financial Foundation: Emergency Funds and Debt Management**
Here are three possible section headlines for your article on budgeting tips for managing personal finances effectively:
Effective budgeting is the cornerstone of financial stability and can significantly impact your overall financial health. Here are three key strategies to help you manage your personal finances more effectively:
1. **Create a Realistic Budget**: Start by tracking your income and expenses to understand your financial situation better. Categorize your spending into fixed (like rent and utilities) and variable expenses (like dining out and entertainment). Use this information to create a budget that reflects your actual spending habits. Make sure to allocate a portion of your income for savings and debt repayment. Tools like budgeting apps or spreadsheets can simplify this process and help you stay organized.
2. **Prioritize Your Financial Goals**: Once you have a budget in place, identify your short-term and long-term financial goals. Whether it's saving for a vacation, buying a home, or planning for retirement, prioritizing these goals will help you allocate your resources effectively. Break down larger goals into smaller, actionable steps, and set deadlines to keep yourself accountable. This approach not only provides motivation but also helps you stay focused on your financial objectives.
3. **Review and Adjust Regularly**: Your financial situation can change due to various factors, such as a new job, a change in expenses, or unexpected costs. Regularly reviewing your budget allows you to make necessary adjustments and stay on track. Consider doing monthly check-ins to assess your progress towards your goals and identify areas where you can cut back or reallocate funds. This proactive approach ensures that your budget remains relevant and effective in managing your finances.
By implementing these strategies, you can take control of your personal finances, build a solid foundation for your financial future, and achieve your long-term goals.
1. **Building a Strong Financial Foundation: Emergency Funds and Debt Management**
Building a strong financial foundation is essential for achieving long-term financial security. Two critical components of this foundation are establishing an emergency fund and managing debt effectively.
An emergency fund serves as a financial buffer that can protect you from unexpected expenses, such as medical emergencies, car repairs, or job loss. Ideally, this fund should cover three to six months' worth of living expenses. To build your emergency fund, start by setting a specific savings goal and create a separate savings account dedicated to this purpose. Contribute regularly, even if it's a small amount, and consider automating these transfers to ensure consistency. Over time, your emergency fund will provide peace of mind and financial stability.
On the other hand, effective debt management is crucial for maintaining a healthy financial life. High levels of debt can hinder your ability to save and invest, making it important to develop a strategy for paying it off. Start by listing all your debts, including interest rates and minimum payments. Prioritize paying off high-interest debts first, as they can accumulate quickly and cost you more in the long run. Consider methods like the debt snowball (paying off smaller debts first for motivation) or the debt avalanche (focusing on the highest interest rates). Additionally, make it a goal to avoid accumulating new debt while you're in the repayment process.
Together, a well-funded emergency fund and a solid debt management plan create a robust financial framework. This foundation not only helps you navigate life's uncertainties but also allows you to focus on future financial goals, such as saving for retirement and investing in personal growth. By prioritizing these elements, you can enhance your overall financial well-being and work towards greater financial independence.
Managing personal finances effectively is crucial for achieving financial stability and security. One of the foundational elements of a solid financial plan is building an emergency fund. This fund acts as a safety net, providing peace of mind and financial security in unexpected situations, such as medical emergencies or sudden job loss. A good rule of thumb is to aim for three to six months' worth of living expenses, which can be achieved by setting up a separate savings account and consistently contributing to it, even if it’s a small amount each month.
Another important aspect of personal finance management is addressing debt. Strategies for paying off debt include the snowball method, where you focus on paying off the smallest debts first to build momentum, or the avalanche method, which prioritizes debts with the highest interest rates to minimize overall interest paid. Improving your credit score is also vital, as it affects your ability to secure loans and favorable interest rates. Regularly checking your credit report, making timely payments, and reducing credit card balances can help enhance your score over time.
Retirement planning should begin as early as possible, regardless of age. Contributing to retirement accounts like a 401(k) or an IRA not only prepares you for the future but can also yield tax benefits. Many employers offer matching contributions, which is essentially free money, making it imperative to take full advantage of this benefit.
Investing in yourself through education and skill-building can lead to increased earning potential and career advancement. This can include formal education, online courses, or even workshops and seminars. The more you invest in your skill set, the better positioned you will be in the job market.
Smart financial planning can also lead to potential tax savings. Familiarizing yourself with deductions and credits available to you, contributing to retirement accounts, and consulting with a tax professional can help you minimize your tax burden.
Insurance plays a crucial role in protecting your financial future. Adequate coverage for health, home, auto, and life insurance can prevent financial devastation in the face of unexpected events.
Finally, setting and achieving long-term financial goals requires careful planning and discipline. Start by defining clear, measurable goals—whether it's buying a home, funding education, or saving for retirement—and develop a strategy to reach them. Regularly reviewing and adjusting your budget, savings, and investment plans will help ensure you stay on track toward achieving your financial aspirations.
In conclusion, effectively managing personal finances requires a holistic approach that encompasses various key aspects, from establishing a solid budget to prioritizing an emergency fund and addressing debt. By taking proactive steps to build financial security, individuals can safeguard themselves against unexpected expenses and cultivate a healthier financial future. Improving credit scores and planning for retirement are essential elements that contribute to long-term stability and growth. Moreover, investing in personal education and skills not only enhances earning potential but also fosters resilience in an ever-changing job market.
Smart financial planning, including strategies for tax savings, ensures that individuals can maximize their resources while minimizing liabilities. Finally, understanding the role of insurance provides an additional layer of protection, allowing for peace of mind in the face of uncertainties. By setting clear, achievable long-term financial goals and regularly reviewing progress, anyone can navigate the complexities of personal finance with confidence. Adopting these budgeting tips will empower you to take control of your financial journey and work toward a secure and prosperous future.