Refractory Metals Unveiled: Exploring High-Heat-Resistant Metals and Their Industrial Applications
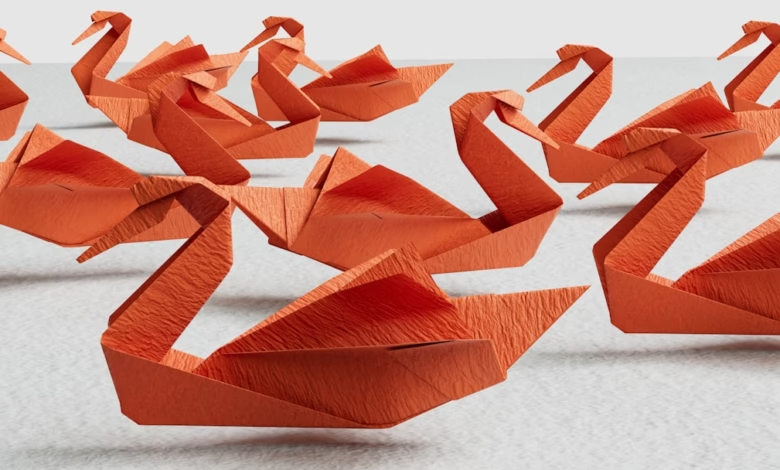
In the ever-evolving landscape of metallurgy, refractory metals like tungsten and molybdenum stand out due to their exceptional high-heat resistance and durability. Unlike traditional ferrous and non-ferrous metals, refractory metals are designed to withstand extreme temperatures, making them indispensable in various industrial applications, from aerospace to energy sectors. As industries increasingly focus on sustainable metal production and metal recycling, understanding the unique properties and roles of refractory metals becomes crucial. This article delves into the fundamental characteristics of refractory metals, their applications in modern industry, and how they compare to other precious and base metals. We’ll explore their contributions to sustainable practices in metal fabrication and recycling, as well as the metallurgical nuances that set them apart from common industrial metals like steel, aluminum, and copper. Join us as we navigate through the complexities of refractory metals and their significance in the broader context of metal commodities and emerging metal trends.
- 1. Understanding Refractory Metals: Key Properties and Applications in Industry
- 2. The Role of Refractory Metals in Sustainable Metal Production and Metal Recycling
- 3. Comparing Refractory Metals with Other Industrial and Precious Metals: A Metallurgical Perspective
1. Understanding Refractory Metals: Key Properties and Applications in Industry
Refractory metals are a unique subset of industrial metals known for their exceptional heat resistance and mechanical strength. The primary refractory metals, including tungsten and molybdenum, are characterized by high melting points, durability, and resistance to deformation under extreme temperatures. These properties make them invaluable in various applications across diverse industries.
One of the key applications of refractory metals is in aerospace and automotive sectors, where they are used in components exposed to high temperatures and stress, such as turbine blades and exhaust systems. Their ability to withstand harsh conditions without degrading makes refractory metals essential for energy metals applications, particularly in power generation and thermal management systems.
In metallurgy, refractory metals are often utilized in the production of metal alloys, enhancing the performance characteristics of base metals like steel, aluminum, and copper. These alloys often exhibit improved strength, wear resistance, and corrosion resistance, making them suitable for demanding environments. Furthermore, the increasing trend toward sustainable metal production has led to an interest in metal recycling processes, allowing the recovery and reuse of precious metals like tungsten and molybdenum from scrap materials.
As industries continue to evolve, the demand for refractory metals is expected to rise, particularly in sectors focused on innovative metal fabrication techniques, such as 3D printing metals. This technology allows for the creation of complex geometries that were previously difficult to achieve with traditional manufacturing processes.
In addition to their industrial applications, refractory metals also play a role in the investment landscape, particularly as investors look toward precious metals like platinum and palladium for their value retention and potential growth. While gold investing and silver investing remain popular, the unique properties of refractory metals make them increasingly attractive in the context of metal commodities.
In conclusion, understanding the key properties and applications of refractory metals is vital for leveraging their benefits in various fields. As industries strive for efficiency and innovation, these high-heat-resistant metals will continue to be at the forefront of metal trends, supporting advancements in energy, aerospace, and automotive technologies.
2. The Role of Refractory Metals in Sustainable Metal Production and Metal Recycling
Refractory metals, such as tungsten and molybdenum, play a significant role in the realm of sustainable metal production and metal recycling. As industries increasingly focus on minimizing their environmental impact, these high-heat-resistant metals are becoming essential components in various applications, enhancing the sustainability of both metal mining and metallurgy processes.
One of the key advantages of refractory metals is their exceptional durability and resistance to metal corrosion, which makes them ideal for use in extreme conditions. In aerospace metals and energy metals applications, for instance, tungsten and molybdenum are often utilized in components that require high performance and longevity. This durability not only reduces the frequency of replacements but also decreases the overall demand for raw materials, contributing to more sustainable metal production practices.
In terms of metal recycling, refractory metals are highly valued because they can be efficiently recovered and reused. The recycling of these metals is crucial in addressing the growing demand for precious metals and non-ferrous metals in various industries, including automotive metals and construction metals. By focusing on metal recycling, companies can minimize waste and lower their carbon footprints while ensuring a steady supply of base metals for future manufacturing needs.
Furthermore, refractory metals are often used in metal alloys, enhancing the properties of other metals such as steel, aluminum, copper, and zinc. This not only improves the performance of these alloys but also allows for more efficient recycling processes, as these mixtures can be processed with minimal energy input. As industries adopt advanced technologies such as 3D printing metals, the use of refractory metals will likely expand, offering new opportunities for sustainable practices in metal fabrication.
Overall, the integration of refractory metals into sustainable metal production and recycling efforts aligns with current metal trends, including the focus on battery metals like lithium and the growing interest in gold investing and silver investing. As the market for metal commodities continues to evolve, the role of refractory metals will be crucial in promoting a more sustainable future for the industry.
3. Comparing Refractory Metals with Other Industrial and Precious Metals: A Metallurgical Perspective
When evaluating refractory metals such as tungsten and molybdenum, it is essential to compare them with other categories of metals to understand their unique characteristics and applications better. Refractory metals are distinguished by their exceptional heat resistance, making them invaluable in high-temperature environments like aerospace and energy sectors.
In metallurgy, refractory metals often outperform traditional industrial metals like steel and aluminum when subjected to extreme conditions. While ferrous metals like steel are known for their strength, they tend to lose structural integrity at elevated temperatures. Conversely, non-ferrous metals, including aluminum and copper, also exhibit lower melting points, limiting their use in high-heat applications.
Precious metals such as gold and platinum are often associated with jewelry and gold investing due to their aesthetic appeal and rarity. However, from a metallurgical perspective, they do not share the same high-temperature resilience as refractory metals. This difference is crucial for industries requiring materials capable of withstanding thermal and mechanical stresses without deformation.
Moreover, the increasing focus on sustainable metal production has led to a surge in interest in metal recycling, particularly for base metals and rare earth metals. While metals like lithium and zinc are vital for battery technologies and other applications, they do not possess the same heat resistance as refractory metals. The trend toward 3D printing metals has also opened new avenues for utilizing refractory alloys in innovative ways, allowing for complex geometries that traditional fabrication methods cannot achieve.
In the automotive and aerospace sectors, the performance of refractory metals is unparalleled. These industries rely on materials that maintain their integrity under high temperatures and pressures, making tungsten and molybdenum ideal candidates. Additionally, as energy metals gain prominence in the context of renewable energy and electric vehicles, understanding the metallurgical properties of refractory metals becomes increasingly relevant.
In conclusion, while other industrial and precious metals serve specific purposes within various sectors, refractory metals stand out for their exceptional resistance to heat and wear. Their unique properties position them as indispensable materials in high-performance applications, setting them apart from more commonly used metals. This comparison underscores the importance of selecting the right metal for the intended application, particularly in fields that demand durability and resilience under extreme conditions.
In conclusion, refractory metals such as tungsten and molybdenum play a crucial role in various industries due to their remarkable high-heat resistance and unique metallurgical properties. As we have explored, these metals not only serve critical functions in sustainable metal production and metal recycling but also stand out when compared to other industrial and precious metals. Their applications span across aerospace, automotive, and energy sectors, highlighting their versatility in metal fabrication and construction.
Moreover, as the demand for more efficient and durable materials increases, understanding the advantages of refractory metals becomes essential for industries aiming to innovate and implement sustainable practices. The comparison with base metals, rare earth metals, and even precious metals like gold and platinum underscores the importance of refractory metals in the larger context of metal commodities.
As we look toward the future of metallurgy, trends such as 3D printing metals and advancements in battery metals will likely further elevate the significance of refractory metals. Their resistance to metal corrosion and stability under extreme conditions make them indispensable in developing more resilient metal alloys. Thus, for industries engaged in metal mining, metal recycling, and sustainable practices, refractory metals are not just a choice but a necessity in the quest for innovation and efficiency.
In summary, embracing the potential of refractory metals can lead to significant advancements in various sectors, ultimately contributing to a more sustainable and resilient future in metal production and application.