Refractory Metals: The Essential High-Temperature Allies in Metal Mining and Sustainable Production
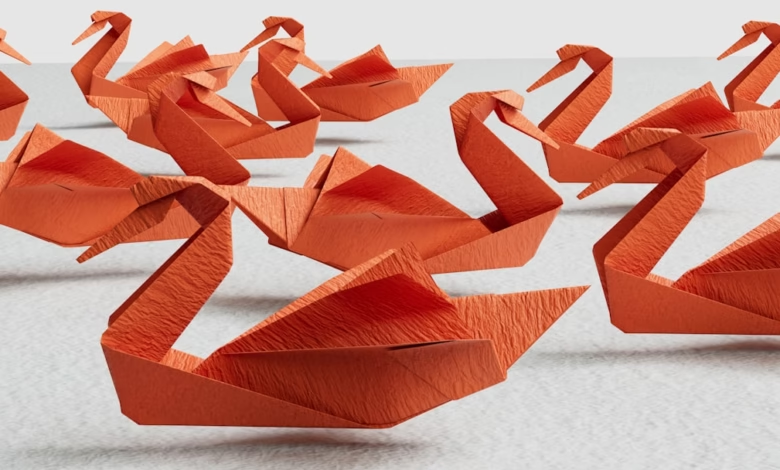
In the ever-evolving landscape of metallurgy, refractory metals stand out as critical components in high-temperature applications, thanks to their exceptional heat resistance and durability. Comprising primarily tungsten and molybdenum, these industrial metals are essential in sectors ranging from aerospace to energy production. As industries increasingly demand materials that can withstand extreme conditions, understanding the unique properties and applications of refractory metals becomes vital. This article delves into the backbone of high-temperature applications, comparing these resilient metals with base and precious metals while highlighting their role in sustainable metal production and recycling efforts. As we explore the future of refractory metals, we will also touch upon their significance in the broader context of metal commodities, metal fabrication, and the emerging trends in metal recycling and sustainable practices. Join us as we uncover the critical role refractory metals play in advancing technology and industry while addressing the challenges posed by metal corrosion and the need for efficient material utilization.
- 1. Understanding Refractory Metals: The Backbone of High-Temperature Applications
- 2. Comparing Refractory Metals with Other Industrial Metals: Tungsten and Molybdenum vs. Base and Precious Metals
- 3. The Future of Refractory Metals in Sustainable Metal Production and Recycling Efforts
1. Understanding Refractory Metals: The Backbone of High-Temperature Applications
Refractory metals, such as tungsten and molybdenum, play a critical role in high-temperature applications across various industries. These metals are characterized by their exceptional resistance to heat and wear, making them indispensable in sectors like aerospace, energy, and automotive. Understanding refractory metals is essential for anyone involved in metallurgy or metal fabrication, as they serve as the backbone for many advanced applications.
In the realm of industrial metals, refractory metals stand out due to their unique properties, including high melting points and excellent thermal stability. This makes them suitable for environments where conventional metals, such as steel, aluminum, or copper, would fail. For instance, in aerospace applications, refractory metals are often used in components that experience extreme temperatures, ensuring reliability and safety in flight operations.
Moreover, refractory metals are increasingly being explored for their potential in metal recycling processes. As industries shift towards sustainable metal production, the ability to reclaim and repurpose these high-performance materials becomes crucial. This trend aligns with the ongoing developments in metal mining and the increasing importance of metal commodities, including rare earth metals and battery metals, in driving technological advancements.
Investors are also taking note of the significance of refractory metals. While gold investing and silver investing remain popular, the unique characteristics of refractory metals are beginning to attract attention within the investment community, particularly in relation to emerging technologies and their applications in 3D printing metals and metal alloys.
As the demand for high-performance materials continues to grow, the role of refractory metals in construction metals and energy metals will likely expand. Their resistance to metal corrosion and ability to withstand high-stress environments position them as key players in future innovations across various industries. Understanding these dynamics is essential for professionals in metallurgy and related fields, as they navigate the evolving landscape of metal trends and applications.
2. Comparing Refractory Metals with Other Industrial Metals: Tungsten and Molybdenum vs. Base and Precious Metals
Refractory metals such as tungsten and molybdenum stand out in the metallurgical landscape due to their exceptional high-heat resistance and durability. When comparing these refractory metals with base and precious metals, notable differences in their properties and applications emerge.
Base metals, including copper, aluminum, zinc, and steel, are widely used in construction, automotive, and energy industries due to their availability and cost-effectiveness. These metals are generally more malleable and ductile, making them ideal for various fabrication processes. However, they tend to have lower melting points and may not perform well in extreme environments, where refractory metals excel.
In contrast, precious metals like gold, platinum, and palladium, while prized for their rarity and aesthetic appeal, are primarily used in jewelry and electronics. Their resistance to corrosion makes them valuable in high-end applications, but they lack the structural integrity required for high-heat applications where tungsten and molybdenum shine.
Refractory metals are integral in aerospace and energy sectors, where components must withstand high temperatures without losing their mechanical properties. For instance, tungsten has the highest melting point of all metals, making it a preferred choice for applications in jet engines and nuclear reactors. Molybdenum, on the other hand, is often used in metal alloys to enhance strength and resistance to thermal expansion.
Additionally, while metal recycling is a significant part of the economy for base and precious metals, the recycling of refractory metals is less common due to their specific applications and the complexities involved in their extraction from metal alloys. The metallurgy of refractory metals also differs, as they require more sophisticated processing techniques, especially in metal mining and sustainable metal production.
As industries continue to evolve, the role of refractory metals is becoming increasingly critical. With trends in 3D printing metals and battery metals gaining traction, tungsten and molybdenum are poised to play important roles in future innovations. Thus, while base and precious metals dominate the market due to their widespread use and investment potential, refractory metals like tungsten and molybdenum carve out a niche where their unique properties are irreplaceable.
In summary, refractory metals offer distinct advantages over base and precious metals in high-performance applications, making them essential for advancements in various fields, from aerospace to energy. Understanding these differences will help industries select the right metals for their specific needs, ensuring both performance and sustainability in metal production.
3. The Future of Refractory Metals in Sustainable Metal Production and Recycling Efforts
The future of refractory metals, particularly tungsten and molybdenum, is poised to play a significant role in sustainable metal production and recycling efforts. As industries shift towards greener practices, the demand for high-heat-resistant metals is increasing, especially in sectors such as aerospace, energy, and automotive. These refractory metals not only possess exceptional thermal stability but also contribute to the development of metal alloys that enhance the performance of various applications.
One of the most promising trends is the integration of refractory metals into metal recycling initiatives. The recycling of industrial metals, including tungsten and molybdenum, can significantly reduce the need for metal mining, which is often resource-intensive and environmentally damaging. By focusing on metal recycling, industries can reclaim precious metals and rare earth metals from end-of-life products, minimizing waste and lowering the carbon footprint associated with new metal production.
Moreover, advancements in metallurgy and 3D printing technologies are enabling more efficient fabrication processes that incorporate refractory metals. This innovation not only optimizes material use but also allows for the creation of complex components with reduced weight and enhanced strength. For instance, in the aerospace sector, the use of refractory metals in lightweight structures can lead to improved fuel efficiency and reduced emissions, aligning with global sustainability goals.
As the market for energy metals, battery metals, and other metal commodities evolves, refractory metals are likely to find new applications in emerging technologies. Their resistance to metal corrosion and high-temperature environments makes them ideal candidates for components in renewable energy systems, such as solar panels and wind turbines. Furthermore, as gold investing and silver investing gain traction, the recycling of jewelry metals and base metals can be enhanced through the inclusion of refractory metals, promoting a circular economy.
In summary, the future of refractory metals in sustainable metal production and recycling is promising. By leveraging their unique properties and integrating them into innovative metal fabrication processes, industries can reduce reliance on virgin materials, support metal recycling efforts, and ultimately contribute to a more sustainable future in metallurgy and metal trends.
In conclusion, refractory metals such as tungsten and molybdenum play a crucial role in high-temperature applications, setting themselves apart from both base and precious metals. Their unique properties make them essential in various industries, from aerospace and automotive to energy sectors, where resistance to heat and corrosion is paramount. As we look to the future, the integration of refractory metals in sustainable metal production and recycling efforts highlights their significance in modern metallurgy.
The ongoing trends in metal recycling and the demand for innovative metal alloys further underscore the importance of these robust materials in meeting the needs of diverse industrial applications. As we navigate the complexities of metal mining and the global landscape of metal commodities, understanding the value of refractory metals will be vital for investors, manufacturers, and researchers alike. By recognizing their potential in the context of emerging technologies, such as 3D printing and battery development, we can better appreciate the pivotal role that refractory metals will continue to play in shaping the future of engineering and manufacturing. Ultimately, an informed approach to investing in metals—whether through gold investing, silver investing, or focusing on energy and automotive metals—will pave the way for a sustainable and resilient metal economy.
References:
– [Insert references as per guidelines]