Refractory Metals: Exploring Tungsten and Molybdenum’s Role in Sustainable Metallurgy and Industrial Applications
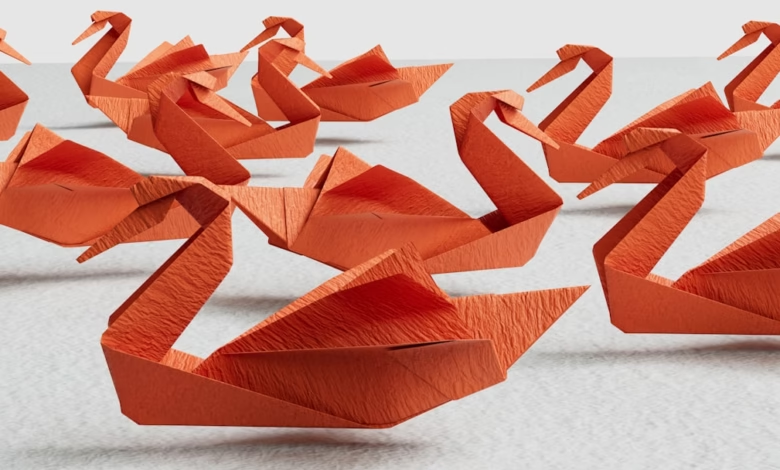
In the ever-evolving landscape of metallurgy, refractory metals like tungsten and molybdenum stand out for their remarkable high-heat resistance and durability. These industrial metals play a pivotal role in various sectors, particularly in aerospace and energy, where performance and reliability are paramount. As the demand for advanced materials continues to grow, understanding the unique properties of refractory metals is essential for industries looking to innovate and enhance their capabilities. This article delves into the significance of tungsten and molybdenum, exploring their applications in modern metallurgy and the burgeoning field of sustainable metal production. We will also examine the future of metal recycling, highlighting practices that promote sustainability in the handling of refractory and precious metals. Join us as we navigate the intricate world of refractory metals and their impact on metal commodities, metal fabrication, and the broader realm of industrial and automotive applications.
- 1. Understanding Refractory Metals: The Role of Tungsten and Molybdenum in Modern Metallurgy
- 2. Industrial Applications of Refractory Metals: Key Players in Aerospace and Energy Sectors
- 3. The Future of Metal Recycling: Sustainable Practices for Refractory and Precious Metals
1. Understanding Refractory Metals: The Role of Tungsten and Molybdenum in Modern Metallurgy
Refractory metals, known for their exceptional resistance to heat and wear, play a crucial role in modern metallurgy, particularly in high-performance applications. Among these, tungsten and molybdenum stand out as two of the most significant refractory metals, each offering unique properties that contribute to various industrial processes.
Tungsten, with the highest melting point of all metals, is often utilized in applications requiring extreme heat resistance, such as aerospace and energy sectors. Its ability to maintain structural integrity under high temperatures makes it invaluable in the manufacturing of aerospace metals and components that can withstand harsh conditions. Additionally, tungsten's density and hardness lend themselves to its use in metal alloys, enhancing the performance of base metals like steel and aluminum in construction and automotive industries.
Molybdenum, while slightly less known than tungsten, is equally important in metallurgy. It is often alloyed with steel to enhance strength, toughness, and resistance to corrosion, making it a critical component in the production of high-strength steel used in construction and automotive applications. Furthermore, molybdenum's role as a catalyst in chemical processes demonstrates its versatility beyond just being a refractory metal.
The significance of these metals extends into the realm of metal recycling, where the demand for sustainable metal production is increasing. As industries seek to reduce their environmental footprint, the recycling of refractory metals, particularly tungsten and molybdenum, is gaining traction. This trend aligns with broader movements in metal mining and sourcing rare earth metals, as industries adapt to the evolving landscape of metal commodities.
In the context of metal trends, the integration of refractory metals into advanced technologies, including 3D printing metals, is reshaping the future of metal fabrication. Their unique properties enable the production of intricate designs and components that were previously unattainable with traditional metalworking methods. As industries continue to invest in innovative processes, tungsten and molybdenum will likely remain at the forefront of developments in metallurgy, from jewelry metals to energy metals.
In summary, understanding the role of refractory metals like tungsten and molybdenum is essential for anyone interested in the current and future landscape of metals, particularly as we navigate the challenges of metal corrosion, sustainability, and the dynamic nature of metal investing. Whether it's through gold investing, silver investing, or exploring the potential of battery metals, these refractory metals contribute significantly to the foundation of modern industrial practices.
2. Industrial Applications of Refractory Metals: Key Players in Aerospace and Energy Sectors
Refractory metals, such as tungsten and molybdenum, play a pivotal role in various industrial applications, particularly in the aerospace and energy sectors. These high-heat-resistant metals are essential for components that must endure extreme temperatures and challenging environments, making them indispensable in modern engineering.
In the aerospace industry, refractory metals are utilized in the production of critical components such as turbine blades, rocket nozzles, and structural elements. These metals are favored for their ability to withstand thermal stress and resist metal corrosion, which enhances the durability and performance of aerospace metals. Companies specializing in aerospace engineering are increasingly turning to advanced metallurgy techniques to create metal alloys that maximize the benefits of refractory metals, ensuring that aircraft and spacecraft can operate efficiently at high altitudes and speeds.
Similarly, the energy sector, especially in areas like nuclear power and high-performance energy generation, relies heavily on refractory metals. Molybdenum is often used in nuclear reactors due to its excellent thermal conductivity and resistance to radiation damage. The energy metals landscape is evolving, with a growing emphasis on sustainable metal production practices. Industries are exploring ways to incorporate metal recycling initiatives to reduce waste and improve resource efficiency, thereby aligning with global sustainability goals.
Key players in these sectors are also investigating the integration of refractory metals in emerging technologies such as 3D printing metals. This innovative approach allows for the creation of complex geometries and customized components that traditional manufacturing methods may not easily achieve. As metal fabrication techniques advance, the demand for high-performance refractory metals is expected to rise, further solidifying their importance in aerospace and energy applications.
In conclusion, refractory metals serve as crucial components in the aerospace and energy industries, where their unique properties contribute to advancements in technology and sustainability. As the market for industrial metals continues to grow, particularly in sectors like aerospace and energy, the role of these high-heat-resistant metals will become even more prominent. The intersection of metal mining, metallurgy, and innovative recycling practices ensures that these valuable resources are utilized efficiently, paving the way for a more sustainable future.
3. The Future of Metal Recycling: Sustainable Practices for Refractory and Precious Metals
As the demand for refractory metals and precious metals continues to rise, the future of metal recycling is evolving towards more sustainable practices. In the context of industrial and non-ferrous metals, recycling is not just an environmental necessity but also an economic imperative. The global push for sustainable metal production has led to innovative methods in metal recycling that can significantly reduce the environmental impact of metal mining.
Refractory metals like tungsten and molybdenum, known for their high-temperature resistance, are increasingly being recycled to meet the needs of various sectors, including aerospace and automotive industries. These metals, along with other precious and rare earth metals, are critical components in high-performance applications. Implementing effective recycling practices ensures that these valuable materials remain in circulation, minimizing the need for new mining operations.
One of the key trends in metal recycling is the growing integration of advanced technologies such as 3D printing metals. This technology not only allows for the efficient fabrication of metal alloys but also enables the recycling of metal scraps into new products, reducing waste. For example, by recycling base metals like copper, aluminum, and zinc, manufacturers can create new construction metals and automotive metals while conserving energy and resources.
Moreover, as gold investing and silver investing continue to attract attention, the recycling of jewelry metals becomes increasingly important. By reclaiming precious metals from old jewelry, we can contribute to a more circular economy that benefits both the environment and the economy. This approach not only helps mitigate metal corrosion but also supports the sustainability of metal commodities in the market.
In the realm of energy metals and battery metals, the recycling of lithium, platinum, and palladium is crucial for meeting the growing demand for high-performance batteries and sustainable energy solutions. As the automotive industry transitions towards electric vehicles, the recycling of these metals will play a pivotal role in reducing the carbon footprint associated with metal fabrication and production.
In conclusion, the future of metal recycling is set to embrace sustainable practices that prioritize the recovery of refractory and precious metals. By leveraging advanced technologies and promoting a circular economy, we can ensure that metal trends align with environmental goals while meeting the demands of various industries. This commitment to sustainable metal production not only preserves our natural resources but also fosters innovation in metallurgy, paving the way for a greener future.
In conclusion, refractory metals like tungsten and molybdenum play a crucial role in modern metallurgy, particularly in high-performance applications within the aerospace and energy sectors. As industries continue to evolve, the demand for these industrial metals is anticipated to rise, driven by their unique properties that withstand extreme heat and stress. Moreover, the future of metal recycling offers promising opportunities for sustainable practices, ensuring that these precious metals and rare earth metals can be efficiently repurposed, reducing the need for new metal mining.
As we look towards a future increasingly focused on sustainability, the integration of metal recycling and innovative methods like 3D printing metals will be pivotal. This not only supports the conservation of valuable resources but also aligns with the trends towards sustainable metal production. Industries must remain vigilant in their approach to metal fabrication and the use of construction metals to mitigate metal corrosion and prolong the lifespan of their products.
Investors in gold, silver, and other metal commodities should also consider the implications of these advancements on market dynamics, particularly as the demand for battery metals and automotive metals continues to rise. As we navigate this ever-changing landscape, understanding the intricacies of refractory metals and their applications will be essential for future success in metallurgy and beyond.