Exploring Refractory Metals: High-Heat-Resistant Industrial Metals Driving Innovation in Aerospace and Energy
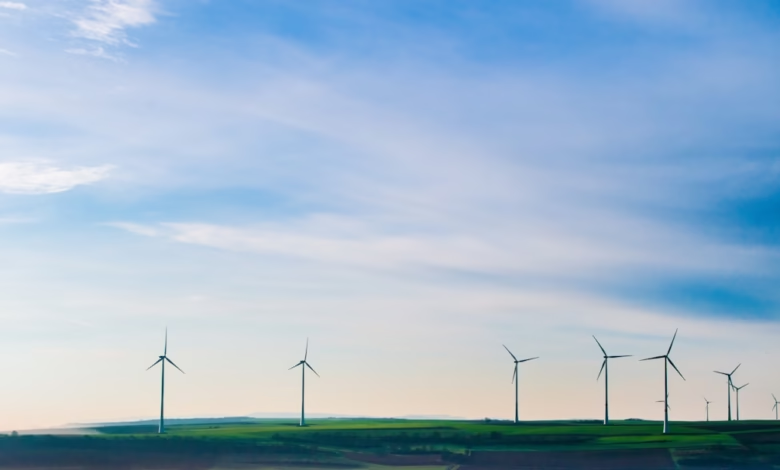
Refractory metals, known for their exceptional high-heat resistance, play a crucial role in modern metallurgy and various industrial applications. Metals such as tungsten and molybdenum are not only vital for their unique characteristics but also for their ability to withstand extreme temperatures, making them indispensable in sectors like aerospace, energy, and automotive industries. As the demand for sustainable metal production rises, understanding the properties and applications of refractory metals has never been more important. This article will delve into the fascinating world of refractory metals, exploring their characteristics and applications, their pivotal role in innovations within the aerospace and energy sectors, and the emerging trends in sustainability and metal recycling practices. With a focus on how these industrial metals fit into the broader landscape of metal commodities, including precious and base metals, we aim to provide a comprehensive overview that highlights the significance of refractory metals in our modern economy. Whether you are involved in metal fabrication, gold investing, or simply interested in the latest metal trends, this exploration of refractory metals will illuminate their importance in the future of metallurgy and sustainable practices.
- 1. Understanding Refractory Metals: Characteristics and Applications in Modern Metallurgy
- 2. The Role of Refractory Metals in Aerospace and Energy Industries: Innovations and Trends
- 3. Sustainability in Metal Production: The Future of Refractory Metals and Recycling Practices
1. Understanding Refractory Metals: Characteristics and Applications in Modern Metallurgy
Refractory metals are a unique category of high-heat-resistant metals, primarily consisting of tungsten, molybdenum, tantalum, and niobium. These metals are characterized by their exceptional melting points, mechanical strength, and resistance to thermal and chemical degradation. This makes them invaluable in modern metallurgy, particularly in applications that require materials to withstand extreme conditions.
One of the most significant characteristics of refractory metals is their ability to maintain structural integrity at elevated temperatures. For example, tungsten, with a melting point of about 3,422°C (6,192°F), is often used in aerospace metals and energy metals applications, where durability and resistance to heat are critical. Similarly, molybdenum’s high melting point and low thermal expansion make it an ideal choice for components in the automotive and aerospace industries, as well as in various metal fabrication processes.
In addition to their thermal resistance, refractory metals are also resistant to metal corrosion, making them suitable for use in harsh environments. This property enhances their longevity and reliability, thus reducing the need for frequent replacements and promoting sustainable metal production practices. The ability to recycle these metals is also a vital aspect of their application, as metal recycling helps minimize waste and supports a circular economy within the realm of industrial metals.
Moreover, refractory metals play a crucial role in the development of metal alloys, enhancing the performance of base metals like steel, aluminum, and copper. By combining these high-performance metals with more common materials, manufacturers can create stronger, more resilient alloys that meet the demands of various industries, including construction metals and jewelry metals.
As the demand for advanced materials continues to rise, particularly in the fields of energy storage and battery technologies, refractory metals are increasingly being explored for their potential in next-generation metal commodities. Their unique properties make them suitable candidates for applications in lithium-ion batteries, where high thermal stability is paramount. Additionally, their role in 3D printing metals technology has gained attention, allowing for the creation of complex geometries that were previously unattainable.
In summary, understanding refractory metals and their characteristics is essential for leveraging their applications in modern metallurgy. As industries evolve and the demand for high-performance materials grows, the significance of refractory metals in metal mining, metal trends, and sustainable practices will only continue to increase.
2. The Role of Refractory Metals in Aerospace and Energy Industries: Innovations and Trends
Refractory metals, such as tungsten and molybdenum, play a pivotal role in both the aerospace and energy industries due to their exceptional heat resistance and durability. As the demand for high-performance materials grows, these industrial metals are increasingly being integrated into innovative applications that require superior thermal stability and mechanical strength.
In the aerospace sector, refractory metals are used extensively in components that must withstand extreme temperatures and stress, such as turbine blades and rocket nozzles. The need for lightweight yet robust materials has led to advancements in metal alloys that incorporate refractory metals, enhancing performance while reducing weight. These aerospace metals are essential for improving fuel efficiency and overall aircraft performance, thus aligning with current trends towards sustainability in aviation.
In the energy sector, refractory metals are critical in applications like nuclear reactors and gas turbines. Their ability to resist metal corrosion under high temperatures makes them ideal for environments where other metals, including base metals like steel and aluminum, may fail. Innovations in metallurgy have led to the development of new refractory metal composites that enhance thermal conductivity and energy efficiency, further pushing the boundaries of energy production technologies.
Furthermore, metal recycling has become increasingly relevant in both industries. The recycling of precious metals and refractory metals not only helps reduce waste but also aligns with sustainable metal production practices. This trend is particularly important as industries look to minimize their environmental impact while ensuring a steady supply of materials for future manufacturing needs.
As we look to the future, the integration of 3D printing metals is revolutionizing how refractory metals are utilized. This innovative manufacturing technique allows for the creation of complex geometries and customized components that were previously unattainable with traditional metal fabrication methods. This trend not only enhances design freedom but also contributes to the efficient use of materials, reducing scrap and supporting sustainable practices.
Overall, the role of refractory metals in the aerospace and energy industries is set to expand as advancements in technology and metallurgy continue to evolve. Their unique properties make them indispensable in the pursuit of efficiency and innovation, solidifying their position as essential components in the landscape of modern industrial applications.
3. Sustainability in Metal Production: The Future of Refractory Metals and Recycling Practices
As the demand for high-heat-resistant metals like tungsten and molybdenum continues to grow, the focus on sustainability in metal production becomes increasingly critical. Refractory metals, known for their exceptional thermal stability and strength, play a pivotal role in various industries, including aerospace, automotive, and energy sectors. However, the environmental impact of metal mining and production processes has raised concerns about the sustainability of these precious and industrial metals.
Sustainable metal production involves adopting practices that minimize the ecological footprint of metal extraction and fabrication. One of the most promising strategies is metal recycling, which significantly reduces the need for raw material extraction. By recycling refractory metals, we can conserve rare earth metals and base metals, decrease energy consumption, and mitigate metal corrosion, all while maintaining the quality and integrity of the materials. This shift toward metal recycling not only supports the circular economy but also helps stabilize metal commodities prices in the market.
In addition to recycling, advancements in metallurgy and 3D printing metals are paving the way for more sustainable practices. Innovative manufacturing techniques allow for the production of metal alloys with enhanced properties while using less material. This approach reduces waste and energy consumption, making the production of construction metals and aerospace metals more efficient. Furthermore, as the industry moves toward greener technologies, the integration of battery metals like lithium and zinc into metal fabrication processes is gaining attention, promoting sustainability in energy applications.
Looking ahead, the future of refractory metals lies in the balance of high-performance applications and sustainable practices. As metal trends evolve, the industry must embrace responsible sourcing, recycling initiatives, and innovative production methods to ensure that we can meet the demands of gold investing, silver investing, and other metal commodities without compromising our planet’s health. By prioritizing sustainable metal production, we can secure a more resilient and environmentally friendly future for all types of metals, from ferrous to non-ferrous, while continuing to support the growing demand in various sectors.
In conclusion, refractory metals such as tungsten and molybdenum play a pivotal role in various industries due to their remarkable high-heat resistance and durability. As we've explored, these industrial metals are not only essential in modern metallurgy but also drive innovations in aerospace and energy sectors, where their unique properties contribute to advancements in technology and efficiency.
The future of refractory metals is closely tied to sustainability, with an increasing emphasis on metal recycling and sustainable metal production practices. As industries shift towards more eco-friendly approaches, the recycling of these precious metals and non-ferrous metals will become vital in reducing waste and conserving resources.
With ongoing developments in metal fabrication, including 3D printing metals and the integration of rare earth metals, we are witnessing a transformation in how refractory metals are utilized. This evolution opens new avenues for gold investing and silver investing, particularly in applications that require enhanced performance and resilience. As we look ahead, the trends in metallurgy, alongside the demand for battery metals and energy metals, will significantly influence the landscape of metal commodities and the overall market for construction metals, automotive metals, and other essential alloys.
Ultimately, understanding the significance of refractory metals not only highlights their crucial role in various applications but also underscores the importance of adopting sustainable practices in metal mining and production. By prioritizing these approaches, we can ensure a more responsible and innovative future for the metal industry.
References:
[Include your references here in APA format]