Exploring Aerospace Metals: The Advantages of Titanium and Innovations in Sustainable Metal Production
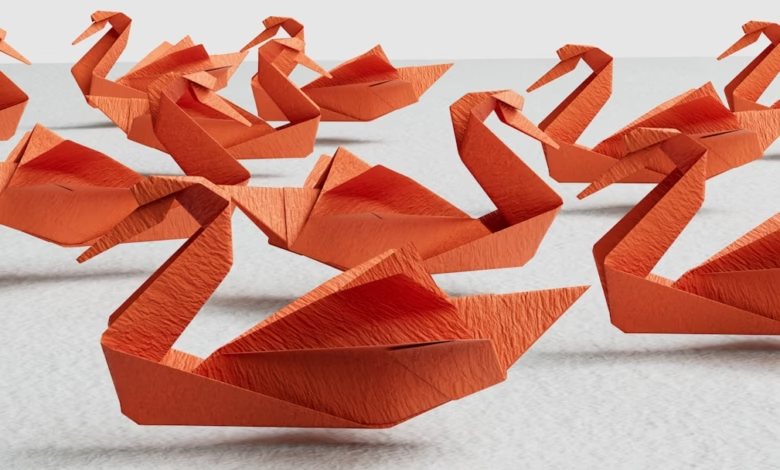
In the ever-evolving world of aerospace engineering, the demand for lightweight yet durable materials has never been greater. As the industry pushes the boundaries of innovation, aerospace metals have emerged as critical components in the quest for efficiency and performance. Among these, titanium and its alloys stand out due to their unique combination of strength, lightweight properties, and resistance to metal corrosion, making them ideal for aviation applications. In this article, we will explore the role of lightweight aerospace metals, specifically focusing on titanium, while comparing it to other industrial metals such as aluminum. Additionally, we will delve into the advancements in sustainable metal production that are transforming the sector, highlighting the importance of metal recycling and the impact of innovative practices on the utilization of precious and rare earth metals. With a clear understanding of these trends, we can appreciate how metallurgy and metal fabrication are revolutionizing the aerospace industry and paving the way for a more sustainable future.
- 1. The Role of Lightweight Aerospace Metals: Exploring Titanium and Its Alloys in Aviation
- 2. Comparing Industrial Metals: Titanium vs. Aluminum in Aerospace Applications
- 3. Sustainable Metal Production: Innovations in Aerospace Metals and Their Impact on Metal Recycling
1. The Role of Lightweight Aerospace Metals: Exploring Titanium and Its Alloys in Aviation
Lightweight aerospace metals play a crucial role in modern aviation, with titanium and its alloys leading the charge in the quest for improved performance and efficiency. As the aerospace industry continues to evolve, the demand for materials that are not only lightweight but also durable has become paramount. Titanium, a non-ferrous metal, is renowned for its exceptional strength-to-weight ratio, making it an ideal choice for various aerospace applications.
The unique properties of titanium alloys, which include corrosion resistance and high-temperature performance, allow for their use in critical components such as aircraft frames, engines, and landing gear. Unlike ferrous metals, which are prone to rust and deterioration, titanium's resistance to metal corrosion enhances the longevity and reliability of aerospace structures. This is particularly important in aviation, where safety and performance are non-negotiable.
Furthermore, titanium is classified as a base metal, yet it is often considered a precious metal due to its rarity and value in specialized applications. The integration of titanium in aerospace design not only contributes to weight reduction but also promotes sustainable practices in metal production. With an increased focus on sustainable metal production methods, the aerospace industry is exploring innovative techniques, including metal recycling and 3D printing metals, to minimize waste and reduce the environmental impact of metal mining.
In addition to titanium, other alloys such as aluminum and certain refractory metals are utilized in aerospace applications, contributing to the overall performance of aircraft. These metals, along with lithium and other energy metals, are integral to the development of advanced systems that require lightweight and strong materials. As the industry continues to embrace new metal trends and advancements in metallurgy, the future of aerospace metals looks promising, paving the way for more efficient and sustainable aviation solutions.
With the ongoing research into metal alloys and the potential for using rare earth metals in aerospace, the field is poised for significant growth. As we witness the rise of innovative metal fabrication techniques, the importance of lightweight aerospace metals, particularly titanium, will only increase, leading to exciting developments in both aviation technology and environmental stewardship.
2. Comparing Industrial Metals: Titanium vs. Aluminum in Aerospace Applications
When it comes to aerospace applications, the choice of metals is critical for ensuring performance and safety. Two of the most commonly used industrial metals in this field are titanium and aluminum, each offering distinct advantages and disadvantages.
Titanium is renowned for its exceptional strength-to-weight ratio, making it one of the most sought-after aerospace metals. It is a non-ferrous metal, meaning it does not contain iron, which contributes to its outstanding resistance to metal corrosion and fatigue. Titanium alloys, which combine titanium with other elements, enhance its properties even further. This metallurgy allows for the development of lightweight components that can withstand extreme temperatures and stress, critical for aerospace applications. However, titanium is relatively expensive, which can pose challenges in terms of cost-effectiveness, especially in large-scale production.
On the other hand, aluminum is one of the most widely used base metals in the aerospace sector. Its lightweight nature, coupled with good strength and excellent workability, makes it an ideal choice for constructing aircraft bodies and wing structures. Aluminum is also highly recyclable, aligning with sustainable metal production practices that are increasingly important in today’s industrial landscape. The availability and lower cost of aluminum compared to titanium make it a popular choice among manufacturers, especially for projects that prioritize budget constraints.
Despite these advantages, aluminum has limitations, particularly in terms of high-temperature performance compared to titanium. While aluminum can be alloyed with other metals like copper and zinc to enhance its properties, it still falls short in scenarios where durability and strength are paramount. In contrast, titanium's performance in harsh conditions often justifies its higher price, particularly in applications where safety and reliability cannot be compromised.
In summary, the choice between titanium and aluminum in aerospace applications largely depends on specific project requirements, including performance criteria, budget, and sustainability goals. As the aerospace industry continues to evolve, trends in metal recycling and advancements in metal fabrication techniques are likely to provide new opportunities for optimizing the use of both titanium and aluminum, alongside other industrial metals. Understanding the unique benefits and challenges of these metals is essential for engineers and manufacturers striving to meet the demands of modern aerospace design and production.
3. Sustainable Metal Production: Innovations in Aerospace Metals and Their Impact on Metal Recycling
Sustainable metal production is becoming increasingly vital in the aerospace industry, particularly as the demand for lightweight and durable materials like titanium and aluminum continues to rise. Innovations in metallurgy and metal fabrication processes are paving the way for more efficient production methods that not only enhance the performance of aerospace metals but also promote sustainability.
One significant development is the focus on recycling industrial metals, which includes both ferrous and non-ferrous metals. By implementing advanced metal recycling techniques, manufacturers can reduce the need for raw metal mining, minimizing environmental impact and conserving precious resources. For instance, the recycling of aluminum not only saves energy but also reduces greenhouse gas emissions, making it a preferred choice among aerospace engineers.
Moreover, the integration of 3D printing metals into aerospace applications introduces new avenues for sustainable production. This method allows for the creation of complex metal alloys with minimal waste, significantly lowering the carbon footprint associated with traditional manufacturing processes. In addition, using recycled materials in 3D printing can further enhance the sustainability of aerospace metals, as it promotes the circular economy within the industry.
The impact of sustainable metal production extends beyond just aerospace applications. The principles applied in aerospace metals can also influence other sectors, such as automotive and construction metals, where the focus on metal recycling and the use of energy metals like lithium and copper is crucial. As the market for metal commodities continues to evolve, investors in gold, silver, platinum, and palladium can benefit from understanding these trends, particularly as they relate to the production and recycling of valuable base metals.
In conclusion, the innovations in sustainable metal production not only boost the efficiency and durability of aerospace metals but also contribute significantly to the broader goal of reducing waste and promoting responsible metal sourcing. As the aerospace industry continues to adopt these practices, the potential for enhanced metal recycling methods will play a critical role in shaping the future of metallurgy and the overall landscape of metal production.
In conclusion, the significance of lightweight and durable aerospace metals, particularly titanium and its alloys, cannot be overstated in modern aviation. As we've explored, these non-ferrous metals offer superior strength-to-weight ratios, making them ideal for reducing fuel consumption and enhancing aircraft performance. The comparison between titanium and aluminum highlights not only their respective advantages but also the ongoing evolution in the selection of industrial metals for aerospace applications.
Moreover, the push for sustainable metal production and innovative practices in metal recycling is paving the way for a more eco-friendly future in the aerospace industry. By embracing advanced metallurgy techniques and efficient metal fabrication methods, we are witnessing a transformation that not only conserves precious resources but also supports the growing demand for energy metals and battery metals essential for future technologies.
As we look ahead, staying informed about metal trends, including the role of rare earth metals and refractory metals, will be crucial for stakeholders in the aerospace sector. The integration of 3D printing metals and the potential for new metal alloys will further revolutionize how we approach aerospace design and construction. Ultimately, the continued investment in research and development will ensure that aerospace metals remain at the forefront of innovation, supporting not only aviation but also advancements in automotive and energy sectors.
References:
[Include relevant citations here]