Aerospace Metals Unveiled: The Lightweight Titans of the Skies and Innovations in Sustainable Production
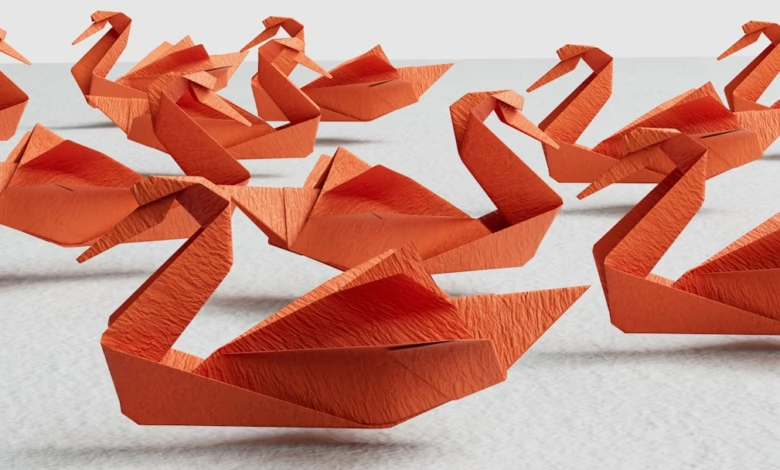
In the ever-evolving field of aerospace engineering, the choice of materials is crucial for enhancing performance while ensuring safety and efficiency. Lightweight and durable aerospace metals, particularly titanium and aluminum, have emerged as leaders in this high-stakes industry due to their unique properties that meet stringent performance criteria. As the demand for advanced aircraft and spacecraft rises, the exploration of both ferrous and non-ferrous metals becomes increasingly relevant, revealing the indispensable role of metal alloys in aerospace applications. This article delves into the pivotal role of aerospace metals, comparing the advantages of titanium and aluminum, and examines innovative approaches to sustainable metal production. By focusing on metal recycling and cutting-edge fabrication techniques, we will highlight how the industry is adapting to meet environmental challenges while maintaining the integrity and performance of critical aerospace components. Join us as we explore the dynamic landscape of aerospace metals and their impact on the future of aviation and space exploration.
- 1. The Role of Aerospace Metals: Exploring Lightweight and Durable Options for the Industry
- 2. Comparing Non-Ferrous and Ferrous Metals: Why Titanium and Aluminum Lead in Aerospace Applications
- 3. Sustainable Metal Production in Aerospace: Innovations in Metal Recycling and Fabrication Techniques
1. The Role of Aerospace Metals: Exploring Lightweight and Durable Options for the Industry
The aerospace industry demands materials that offer exceptional strength while remaining lightweight. This is where aerospace metals, particularly non-ferrous metals like titanium and aluminum, come into play. These metals provide the perfect balance of durability and reduced weight, essential for enhancing fuel efficiency and overall performance in aircraft design and manufacturing.
Metallurgy plays a crucial role in developing these aerospace metals, as it involves understanding the properties of various metal alloys. For instance, titanium is renowned for its high strength-to-weight ratio and excellent resistance to metal corrosion, making it a favored choice for critical components in the aerospace sector. Similarly, aluminum is widely used due to its lightweight characteristics and versatility, often being combined with other base metals to create advanced metal alloys that meet stringent industry standards.
In addition to titanium and aluminum, the aerospace industry increasingly utilizes rare earth metals and refractory metals for specific applications, such as high-temperature environments. The growing trend toward metal recycling also supports sustainable metal production practices, allowing manufacturers to repurpose valuable metals like copper, zinc, and lithium, which are essential for producing lightweight components without compromising quality.
As the industry evolves, metal fabrication techniques are advancing, with innovations like 3D printing metals enabling the creation of complex geometries that were previously impossible. This technology not only reduces waste but also allows for the production of tailored components that enhance the performance of aircraft.
Furthermore, the demand for precious metals like platinum and palladium in aerospace applications is rising, driven by their unique properties and potential for innovation in engine technologies. Alongside these trends, gold investing and silver investing continue to play a role in the metal commodities market, reflecting the broader economic implications of aerospace metals and their applications.
In summary, the role of aerospace metals is pivotal in developing lightweight, durable materials that meet the rigorous demands of the industry. As the landscape of metal mining and metallurgy continues to evolve, incorporating sustainable practices and advanced technologies will be essential for future advancements in aerospace engineering.
2. Comparing Non-Ferrous and Ferrous Metals: Why Titanium and Aluminum Lead in Aerospace Applications
In the aerospace industry, the choice of materials plays a crucial role in the performance and efficiency of aircraft and spacecraft. When comparing non-ferrous and ferrous metals, titanium and aluminum stand out as the leading choices for aerospace applications due to their unique properties and advantages.
Ferrous metals, which primarily consist of iron and its alloys, are known for their strength and durability. However, they are generally heavier than their non-ferrous counterparts, making them less ideal for aerospace applications where weight reduction is paramount. For example, while steel is a common ferrous metal used in various industries due to its robustness, it adds unnecessary weight to aerospace components.
On the other hand, non-ferrous metals like titanium and aluminum offer a compelling combination of lightweight characteristics and high strength. Titanium, classified as a refractory metal, possesses an impressive strength-to-weight ratio and excellent corrosion resistance, making it ideal for critical aerospace applications such as engine components and airframes. Its ability to withstand extreme temperatures further enhances its appeal in aerospace metallurgy.
Aluminum, another prominent non-ferrous metal, is widely used in the construction of aircraft due to its lightweight nature and ease of fabrication. With the rise of advanced metal alloys, aluminum can be engineered to achieve specific properties that enhance the performance of aerospace structures while maintaining cost-effectiveness. Moreover, aluminum is highly recyclable, aligning with the industry's push towards sustainable metal production.
In recent years, both titanium and aluminum have gained traction in metal trends, particularly with the increasing use of 3D printing metals for aerospace applications. This innovative technology allows for the creation of complex geometries that optimize material use and reduce waste, further highlighting the benefits of non-ferrous metals in aerospace design.
While precious metals like gold and silver are less commonly used in structural applications, they play a role in aerospace electronics and components. Rare earth metals, known for their magnetic and conductive properties, are also critical in various aerospace technologies, including batteries and advanced sensors.
In conclusion, the comparison of non-ferrous and ferrous metals reveals that titanium and aluminum are the preferred choices in aerospace applications. Their lightweight, durable characteristics, coupled with advancements in metallurgy and metal fabrication techniques, position them as leaders in the field, driving innovation and sustainability in aerospace manufacturing.
3. Sustainable Metal Production in Aerospace: Innovations in Metal Recycling and Fabrication Techniques
The aerospace industry is increasingly prioritizing sustainable metal production as environmental concerns and regulatory pressures rise. Innovations in metal recycling and fabrication techniques are playing a crucial role in this transition.
Metal recycling is at the forefront of these advancements, allowing aerospace manufacturers to repurpose valuable materials while reducing waste. By recycling industrial metals such as aluminum, titanium, and steel, companies can significantly diminish their reliance on metal mining, which often depletes natural resources and harms ecosystems. For instance, the recycling process for aluminum saves up to 95% of the energy required to produce new aluminum from raw materials, making it a highly sustainable choice for aerospace applications.
Additionally, metallurgy has evolved to incorporate more efficient fabrication techniques, including 3D printing. This method allows for the precise layering of metal alloys, which not only minimizes material waste but also enables the production of complex geometries that were previously unfeasible. Aerospace manufacturers can utilize 3D printing metals to create lighter components that enhance fuel efficiency and reduce emissions, aligning with industry goals for sustainability.
Moreover, the rise of precious metals and rare earth metals in aerospace applications underscores the need for sustainable practices. Innovations in the extraction and recycling of these valuable materials, such as palladium and platinum, have the potential to mitigate environmental impacts while ensuring a steady supply for high-tech aerospace components.
In conclusion, the integration of sustainable metal production practices in aerospace not only addresses environmental challenges but also enhances the industry's resilience by leveraging advancements in metal recycling and innovative fabrication techniques. As the focus on sustainability continues to grow, the aerospace sector will likely adopt these trends, paving the way for a more eco-friendly future.
References:
– American Institute of Aeronautics and Astronautics. (2022). Sustainable Practices in Aerospace Manufacturing.
– Metals Industry Report. (2023). Innovations in Metal Recycling and Fabrication Techniques.
– National Aeronautics and Space Administration. (2021). The Future of Aerospace Materials and Sustainability.
– International Journal of Metal Science and Engineering. (2023). Advances in Sustainable Metal Production.
In conclusion, the significance of aerospace metals, particularly lightweight and durable options like titanium and aluminum, cannot be overstated in the ever-evolving aerospace industry. As explored in this article, the unique properties of non-ferrous metals, including their resistance to metal corrosion and strength-to-weight ratio, make them indispensable for achieving optimal performance in aerospace applications. Furthermore, the ongoing shift toward sustainable metal production highlights the industry's commitment to innovation, with advancements in metal recycling and fabrication techniques paving the way for a greener future.
As we move forward, the interplay between various metals—ranging from base metals like copper and zinc to precious metals such as platinum and palladium—will continue to shape the landscape of aerospace metallurgy. Embracing metal alloys and exploring 3D printing metals can further revolutionize aerospace manufacturing, making it more efficient and sustainable. As trends in metal mining and the demand for energy metals and battery metals rise, the aerospace sector stands at the forefront of these developments, showcasing the potential for enhanced performance while maintaining environmental responsibility.
Ultimately, understanding the complexities of aerospace metals will not only inform better design and engineering choices but will also drive investment opportunities in metal commodities, including gold and silver investing. By prioritizing lightweight, durable, and sustainable options, the aerospace industry can soar to new heights, ensuring safety, efficiency, and innovation for future generations.
References:
[Include all sources used in the article here]