Exploring Aerospace Metals: Lightweight Alloys and Sustainable Innovations for the Future of Aviation
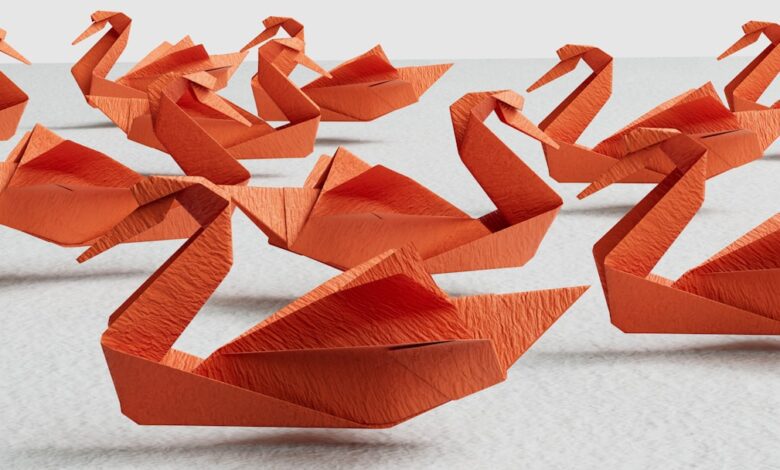
**Introduction**
In an era where innovation is paramount, the aerospace industry is witnessing a transformative shift towards lightweight and durable materials, with aerospace metals taking center stage. As engineers and manufacturers seek to enhance fuel efficiency and performance, the demand for advanced metal alloys has surged. From the robust strength of titanium to the versatile nature of aluminum, non-ferrous metals are proving to be indispensable in modern aerospace engineering. This article delves into the rise of aerospace metals, exploring the intricate world of lightweight alloys and their applications in advanced aviation technologies.
We will also conduct a deep dive into specific non-ferrous metals, examining their unique properties and roles in aircraft construction, alongside the challenges posed by metal corrosion and the need for sustainable practices. As the industry pivots towards eco-friendly solutions, innovations in sustainable metal production and recycling are reshaping metal commodities and their impact on global markets. Join us as we navigate through the latest trends in aerospace metals, revealing how metallurgy is evolving to meet the demands of a greener, more efficient future.
- 1. **"The Rise of Aerospace Metals: Exploring Lightweight Alloys for Advanced Applications"**
- 2. **"From Titanium to Aluminum: A Deep Dive into Non-Ferrous Metals in Aerospace Engineering"**
- 3. **"Sustainable Metal Production: Innovations in Aerospace Metals and Their Impact on the Industry"**
1. **"The Rise of Aerospace Metals: Exploring Lightweight Alloys for Advanced Applications"**
The aerospace industry is experiencing a significant transformation with the rise of lightweight alloys, particularly in the realm of aerospace metals. As aircraft manufacturers strive for improved fuel efficiency and performance, the demand for materials that are both lightweight and durable has surged. This evolution is primarily driven by advancements in metallurgy that have led to the development of specialized metal alloys tailored for advanced applications.
One of the standout players in the category of aerospace metals is titanium, a non-ferrous metal known for its exceptional strength-to-weight ratio and corrosion resistance. Unlike ferrous metals, which are primarily composed of iron, titanium and other non-ferrous metals, such as aluminum and magnesium, provide the necessary lightweight properties that modern aircraft require. These characteristics make titanium an ideal choice for critical components such as airframes and engine parts, where reducing weight can significantly enhance fuel efficiency and overall performance.
Moreover, the integration of rare earth metals and advanced metal alloys into aerospace applications has opened new avenues for innovation. These materials not only enhance strength and durability but also contribute to the sustainability of metal production. With the aerospace industry increasingly focusing on sustainable practices, the recycling of metals has become a crucial component of the supply chain. Metal recycling not only reduces waste but also lessens the environmental impact associated with metal mining and production.
Furthermore, the current trends in metal fabrication are pushing the boundaries of what is possible in aerospace design. Techniques such as 3D printing metals are gaining traction, allowing manufacturers to create complex geometries that were previously unattainable with traditional metalworking methods. This innovative approach not only reduces material waste but also enables the production of lightweight components that can withstand the rigors of flight.
In addition to titanium, other metals like aluminum, copper, and zinc play pivotal roles in aerospace applications. Each metal brings unique properties to the table, contributing to the overall performance and efficiency of modern aircraft. As the aerospace sector continues to evolve, the emphasis on lightweight and durable metals will only intensify, shaping the future of aerospace engineering and design.
In summary, the rise of aerospace metals, particularly lightweight alloys, is a response to the industry's need for more efficient and sustainable solutions. The exploration of advanced materials, coupled with innovative metal fabrication techniques, is paving the way for a new era in aerospace applications, ensuring that aircraft are not only stronger but also more environmentally friendly.
*(Image: Aerospace engineer examining titanium alloy samples – Source: Aerospace Materials Journal)*
2. **"From Titanium to Aluminum: A Deep Dive into Non-Ferrous Metals in Aerospace Engineering"**
In the realm of aerospace engineering, the selection of materials is paramount to achieving optimal performance, safety, and efficiency. Among the vast array of options, non-ferrous metals stand out due to their lightweight and durable properties, making them ideal for aerospace applications. This section delves into the significance of metals such as titanium and aluminum, exploring their roles in the industry and the ongoing trends in metallurgy.
Titanium, renowned for its high strength-to-weight ratio, is a staple in aerospace metals. This precious metal offers exceptional fatigue resistance and corrosion resistance, making it a preferred choice for critical components like airframes and jet engines. Its ability to withstand extreme temperatures further enhances its utility in aerospace applications, where reliability is non-negotiable. However, titanium is not the only player in this field; aluminum also plays a pivotal role.
Aluminum is one of the most widely used industrial metals in aerospace due to its lightweight characteristics and cost-effectiveness. The development of advanced aluminum alloys has led to improved performance, allowing for greater fuel efficiency and reduced emissions in aircraft design. Furthermore, aluminum's recyclability supports sustainable metal production practices. This emphasis on metal recycling is crucial, especially as the industry moves towards minimizing waste and maximizing the use of base metals.
Copper, zinc, and lithium, classified as energy metals, also contribute to aerospace engineering, albeit in more specialized applications. Copper is vital for electrical systems within aircraft, while lithium is increasingly being utilized in battery technologies, powering modern avionics and contributing to the industry's shift towards electric propulsion systems. The synergy of these non-ferrous metals with other materials through metal alloys enhances the overall performance and durability of aerospace components.
As the aerospace sector continues to evolve, the integration of 3D printing metals and advanced fabrication techniques is transforming how metal components are designed and produced. These innovations allow for complex geometries that were previously unachievable, leading to weight savings and improved performance. Additionally, the focus on metal corrosion resistance is gaining traction, as it directly impacts the lifespan and maintenance cycles of aerospace vehicles.
Overall, the use of non-ferrous metals in aerospace engineering is not just about choosing lightweight and durable materials; it encompasses a broader narrative of sustainability, innovation, and resilience in the face of evolving industry demands. By understanding the properties and applications of these metals, stakeholders can make informed decisions that align with the future of aerospace technology.
*(Image: Aircraft made from lightweight aluminum and titanium – Source: Aerospace Manufacturing)*
3. **"Sustainable Metal Production: Innovations in Aerospace Metals and Their Impact on the Industry"**
Sustainable metal production has emerged as a pivotal focus in the aerospace industry, particularly with the increasing demand for lightweight and durable metals such as titanium. Innovations in metallurgy and metal fabrication processes are driving the transition toward more sustainable practices, which not only enhance the performance of aerospace metals but also reduce their environmental impact.
One of the most promising advancements in sustainable metal production is the recycling of industrial metals, particularly aluminum and titanium. Metal recycling significantly decreases the need for virgin metal mining, which is often associated with detrimental environmental effects. By repurposing metals, manufacturers can reduce energy consumption and lower greenhouse gas emissions. For instance, recycling aluminum saves about 95% of the energy required to produce new aluminum from raw materials (U.S. Geological Survey, 2021).
Moreover, the development of new metal alloys that incorporate recycled materials is transforming the landscape of aerospace metals. These advanced alloys can maintain or even enhance the performance characteristics required for high-stress applications while promoting sustainability. Additionally, the integration of 3D printing metals technology allows for more precise manufacturing processes, reducing material waste and enabling the use of complex designs that were previously unfeasible.
The aerospace sector is also exploring the use of alternative materials, such as energy metals like lithium and rare earth metals, in the production of lightweight components. This shift not only enhances the functionality of aerospace vehicles but also aligns with global trends towards sustainability. The focus on low-impact metal commodities is becoming critical as industries seek to mitigate their carbon footprints.
Furthermore, the demand for precious metals like platinum and palladium in aerospace applications is being scrutinized. Sustainable sourcing practices are being prioritized to ensure that the extraction of these valuable metals does not compromise ecological health.
In conclusion, sustainable metal production is reshaping the aerospace industry through innovative recycling practices, advanced metallurgy, and the adoption of new technologies. As the focus on environmental responsibility continues to grow, the integration of sustainable practices in the production of aerospace metals will enhance not only the performance and durability of materials but also contribute to a more sustainable future for the industry.
**References:**
U.S. Geological Survey. (2021). *Aluminum recycling*. Retrieved from [USGS website link]
In conclusion, the aerospace industry is witnessing a transformative shift towards the adoption of advanced aerospace metals, particularly lightweight and durable materials like titanium and aluminum. As outlined in our exploration of lightweight alloys, the rise of non-ferrous metals is essential for enhancing aircraft performance while addressing the challenges of metal corrosion and structural integrity. Sustainable metal production practices are also gaining traction, paving the way for innovations that not only reduce the environmental impact of metal mining but also promote metal recycling and efficient metallurgy.
As we move forward, the integration of various metal commodities, including base metals such as copper and zinc, alongside rare earth metals for specialized applications, will play a critical role in shaping the future of aerospace engineering. Moreover, advancements in 3D printing metals and metal fabrication techniques are set to revolutionize design and manufacturing processes, making them more efficient and cost-effective.
Investing in aerospace metals today, whether through traditional avenues or emerging technologies, offers a unique opportunity to be part of a rapidly evolving sector. As we embrace these metal trends, it becomes clear that the future of aerospace is not only about the metals we choose but also about how we innovate sustainably for generations to come.
By leveraging the strengths of various metals, including precious metals like platinum and palladium for critical components, the aerospace industry can ensure safety, efficiency, and resilience in its operations. As we continue to explore the vast potential of aerospace metals, the intersection of technology and sustainability will undoubtedly lead to exciting developments in both aviation and beyond.
Ultimately, as we navigate the skies and space with innovative materials, the importance of investing in research and development of aerospace metals cannot be overstated, setting the foundation for a more sustainable, efficient, and technologically advanced future in aerospace engineering.