Speculating on Gold Prices: A Deep Dive into Gold Futures and Options for Smart Investment Strategies
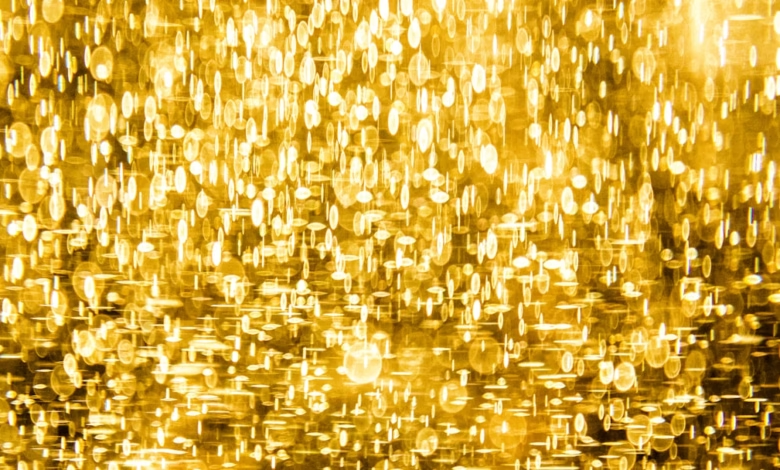
In an ever-evolving financial landscape, gold remains a beacon for investors seeking stability and growth. As a safe haven asset, gold has historically served as a hedge against economic uncertainty, inflation, and market volatility. With the advent of gold futures and options, investors now have innovative ways to engage with gold investment strategies, allowing them to speculate on gold prices without needing to hold physical gold. This article delves into the intricacies of gold futures and options, providing a comprehensive guide to understanding these derivatives and their impact on gold market trends. We will analyze how these financial instruments influence gold prices, investor sentiment, and the overall dynamics of global gold demand. Additionally, we will explore the role of gold amid economic turbulence and the importance of central banks' gold reserves as a stabilizing force. Join us as we navigate the complexities of gold trading and uncover how derivatives can enhance your investment portfolio in an increasingly unpredictable world.
- 1. Understanding Gold Futures and Options: A Comprehensive Guide to Gold Investment Strategies
- 2. Analyzing Gold Market Trends: How Derivatives Influence Gold Prices and Investor Sentiment
- 3. The Role of Gold as a Safe Haven Asset: Navigating Gold Futures Amid Economic Uncertainty
1. Understanding Gold Futures and Options: A Comprehensive Guide to Gold Investment Strategies
Gold investment has long been a popular strategy for both seasoned investors and newcomers looking to diversify their portfolios. Understanding gold futures and options is essential for those who wish to speculate on gold prices through derivatives. These financial instruments offer unique opportunities to capitalize on the fluctuations in the gold market while managing risk effectively.
Gold futures contracts are agreements to buy or sell a specific amount of gold at a predetermined price on a future date. This type of investment is particularly attractive during times of economic uncertainty, as gold is often viewed as a safe haven asset. Investors can benefit from the potential rise in gold prices without having to hold physical gold, which can entail additional costs related to storage and security.
Options on gold futures provide investors with the right, but not the obligation, to buy or sell gold at a specific price within a set timeframe. This flexibility allows traders to hedge against price volatility or speculate on future movements in the gold market. For instance, if an investor believes that gold prices will rise due to inflationary pressures or geopolitical tensions, they might purchase call options to profit from these anticipated increases.
The gold market is influenced by various factors, including global gold demand, central banks' gold reserves, and market trends. Events such as gold mining production levels and advancements in gold technology can also impact prices. Additionally, the rise of gold ETFs (exchange-traded funds) has made gold investment more accessible, allowing individuals to invest in gold bullion without the need for physical ownership.
Another important aspect of gold investment is the role of gold recycling and refining. With sustainable gold mining practices gaining traction, many investors are now considering the environmental impact of their investments. This shift has led to increased interest in gold sourced from responsible mining operations.
Furthermore, the interplay between gold and cryptocurrency has emerged as a significant topic in recent years. As digital currencies gain popularity, many investors are exploring the potential of gold coins and collectibles as a hedge against the volatility of the cryptocurrency market. This diversification strategy can provide a balanced approach to risk management in an increasingly unpredictable financial landscape.
In summary, understanding gold futures and options is crucial for developing effective gold investment strategies. By analyzing gold market trends and leveraging various financial instruments, investors can navigate the complexities of gold trading while capitalizing on the asset's historical stability and potential for growth. Whether through physical gold, gold bars, or derivatives, the gold investment landscape offers numerous opportunities for those willing to explore its intricacies.
2. Analyzing Gold Market Trends: How Derivatives Influence Gold Prices and Investor Sentiment
The gold market is a dynamic environment influenced by various factors, including derivatives such as gold futures and options. These financial instruments allow investors to speculate on gold prices without the need to own physical gold, providing a unique avenue for investment. Analyzing gold market trends reveals how derivatives can shape investor sentiment and impact gold prices.
Gold futures contracts are agreements to buy or sell gold at a predetermined price on a specific date in the future. This mechanism enables traders to hedge against potential price fluctuations. In times of economic uncertainty, such as during periods of inflation or geopolitical instability, gold is often viewed as a safe haven asset. This perception boosts demand for gold futures and can lead to increased gold prices. Central banks also play a crucial role in this dynamic; their gold reserves can influence market sentiment and prices significantly.
Options on gold futures provide an additional layer of flexibility for investors. These derivatives allow traders to speculate on price movements without the obligation to buy or sell the underlying asset. As gold prices rise, investor sentiment often shifts positively, leading to increased activity in gold ETFs and other gold-related investments. This reaction can create a feedback loop where rising prices attract more investors, further driving up gold prices.
The interplay between gold market trends and derivatives is evident during significant economic events. For instance, when inflation is perceived to be rising, the demand for gold bullion and gold bars typically increases, reflecting a shift in investor behavior. Additionally, during such times, the market often sees a rise in gold coin investing and the trading of gold collectibles, as investors seek diverse ways to hold their gold investments.
Furthermore, the relationship between gold and cryptocurrency has gained traction in recent years. As digital currencies become more mainstream, some investors view gold as a traditional hedge against the volatility of cryptocurrencies. This crossover can influence gold market trends, as investors look to balance their portfolios with both physical gold and digital assets.
In conclusion, analyzing gold market trends through the lens of derivatives reveals a complex interaction that significantly influences gold prices and investor sentiment. By understanding these dynamics, investors can make more informed decisions in the ever-evolving landscape of gold investment. Whether through gold mining, gold recycling, or luxury gold collectibles, the derivatives market remains a critical component of the broader gold trading ecosystem.
3. The Role of Gold as a Safe Haven Asset: Navigating Gold Futures Amid Economic Uncertainty
Gold has long been recognized as a safe haven asset, particularly during periods of economic uncertainty. This characteristic makes it an appealing option for investors looking to hedge against market volatility and inflation. The role of gold in the financial landscape has evolved, but its fundamental value remains rooted in its scarcity and intrinsic qualities.
Investing in gold futures allows traders to speculate on the future price of gold without the necessity of holding physical gold. This method can be particularly advantageous during times of economic turmoil when gold prices tend to rise as investors seek refuge from unstable financial markets. For instance, during inflationary periods, gold is often seen as a reliable store of value, as it can help preserve purchasing power when fiat currencies weaken.
The gold market trends reveal that central banks have been increasing their gold reserves as a strategy to bolster their balance sheets against economic shocks. This heightened demand from central banks, along with global gold demand driven by investment and jewelry sectors, influences gold prices significantly. As such, understanding gold market analysis becomes crucial for traders engaging in gold futures.
Moreover, gold ETFs have emerged as a popular investment vehicle, offering a convenient way to gain exposure to gold prices without needing to handle physical gold. This accessibility has broadened the appeal of gold investing, allowing both retail and institutional investors to participate in the gold trade more easily.
Sustainable gold mining practices are also becoming increasingly relevant as consumers and investors alike are more conscious of ethical sourcing. This trend is significant in shaping the future of gold production and refining, as it impacts the overall perception of gold as an investment vehicle.
As the landscape of global finance continues to shift, gold's role as a safe haven asset is likely to persist. Investors should remain vigilant about gold prices and market dynamics, especially as emerging technologies and alternative assets, such as cryptocurrency, further reshape investment strategies. By understanding these factors, investors can navigate the complexities of gold futures effectively and make informed decisions in a fluctuating economic environment.
In conclusion, speculating on gold prices through derivatives such as gold futures and options offers a dynamic approach for investors looking to capitalize on the fluctuations in the gold market. As we have explored, understanding the fundamentals of gold investment strategies is crucial for navigating market trends and making informed decisions. The influence of derivatives on gold prices cannot be overlooked, particularly in how they shape investor sentiment during periods of economic uncertainty.
As a safe haven asset, gold remains a significant player in the financial landscape, especially when considering factors like inflation and global gold demand. Whether you choose to invest in physical gold, gold ETFs, or engage in gold trading through futures and options, it's vital to stay informed about gold reserves, gold refining, and the broader implications of gold production on the market.
With the ongoing evolution of the gold market, including the rise of gold technology and sustainable gold mining practices, investors have a plethora of opportunities to explore. By keeping abreast of gold market analysis and trends, you can strategically position your portfolio to benefit from the enduring allure of gold, be it in the form of gold bullion, gold coins, or luxury gold collectibles. As you navigate the complexities of gold investment, remember that a well-rounded understanding of both the historical significance of gold and its contemporary role in finance will empower you to make the most of your investments.
References:
(Include relevant citations here)